Un métal antichoc imprimé en 3D
Une nouvelle structure métallique en treillis résiste mieux aux impacts.
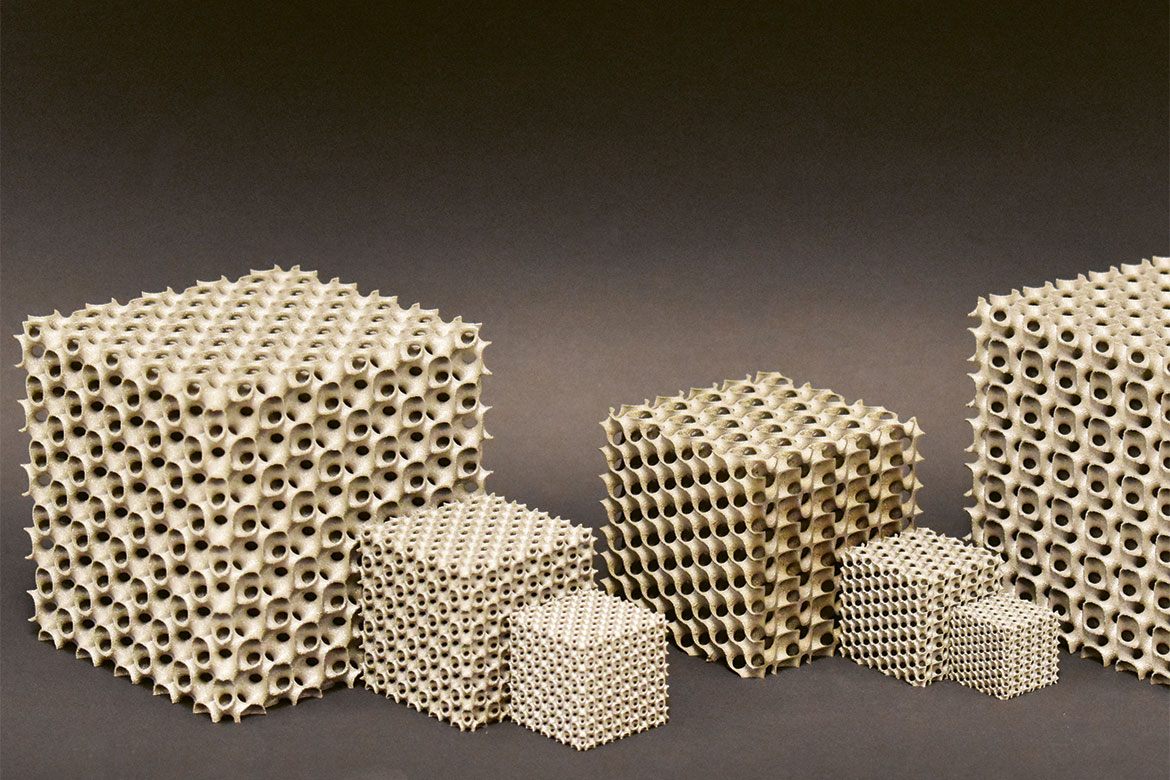
Avec leur arrangement régulier, les trous rendent la structure plus résistante. | Image: Colin Bonatti, Dirk Mohr
L’impression 3D est en plein développement, également pour les métaux. Un laser fusionne de la poudre d’acier, et le fluide est déposé comme dans les procédés conventionnels. C’est ainsi que Dirk Mohr, chercheur à l’ETH Zurich, a conçu un métal en treillis optimisé pour absorber les chocs. Les pleins et les creux sont arrangés de manière répétitive afin de répartir la force des impacts et de réduire les déformations.
Dirk Mohr avait exploré ce sujet pendant ses études, voilà plus de quinze ans. Mais de telles structures tridimensionnelles n’existaient alors que sur le papier: «Il ne s’agissait que d’un pur jeu de l’esprit, irréalisable en pratique. Comme j’ai plutôt une mentalité d’ingénieur, j’avais abandonné ces travaux. Avec l’essor des technologies de manufacture par addition, j’ai pu les ressortir de mes tiroirs.»
Le nouveau matériau rappelle les mousses métalliques, une masse d’acier qui renferme une grande quantité d’air dans de petites chambres. Mais la structure des mousses est plus ou moins aléatoire, car les bulles se forment au hasard par injection de gaz dans le métal en fusion. Au contraire, l’impression 3D permet de contrôler la structure du matériau dans ses moindres détails et d’en maîtriser les propriétés.
Avec son doctorant Colin Bonatti, Dirk Mohr a conçu un matériau isotropique: il résiste de manière égale à la pression et aux impacts dans toutes les directions. Les pores du métal suivent un design en coquille: une structure courbe et complexe, développée sur ordinateur, optimisée pour répartir les impacts et limiter les déformations. Cette approche pourrait servir à concevoir des éléments sur mesure, comme des absorbeurs ultralégers d’énergie mécanique ou des implants biomédicaux, explique le chercheur. «Une production industrielle, par exemple dans l’automobile, devra attendre une baisse des coûts de la manufacture additive métallique.»